How To Keep Small Batch Labels Consistent Between Runs
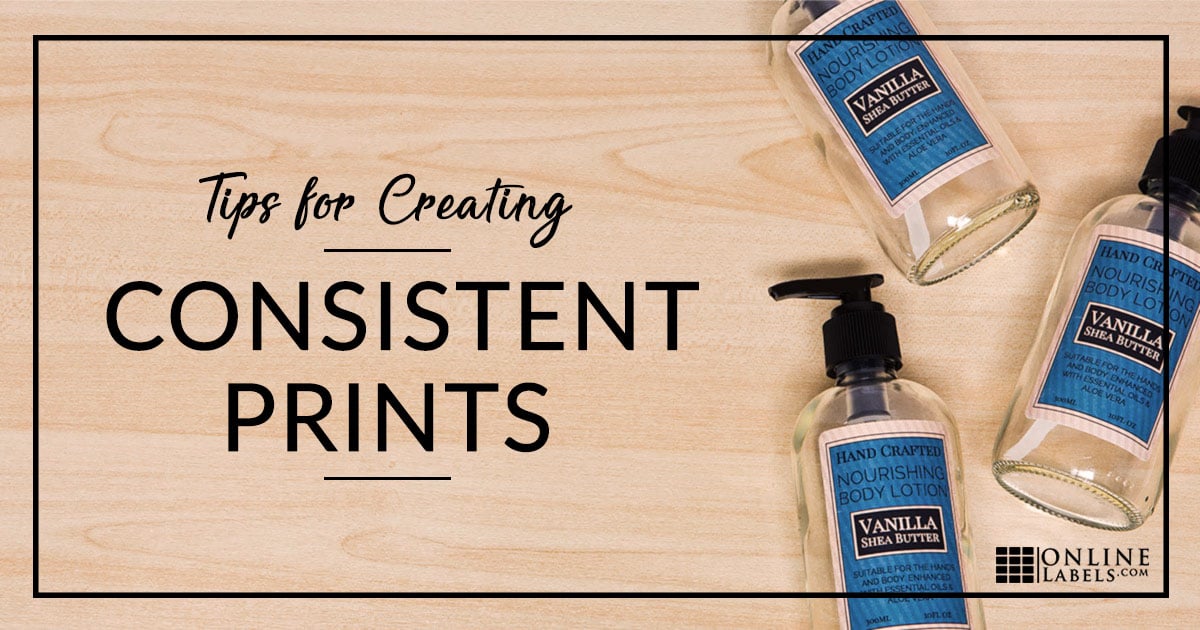
When creating labels for your project or products, it can be hard to ensure consistency across various print runs. Ink cartridge levels vary, papers can shift causing alignment issues, and storage conditions can cause their own issues.
To help keep each run looking like the first, follow these tips.
Store Your Labels Safely
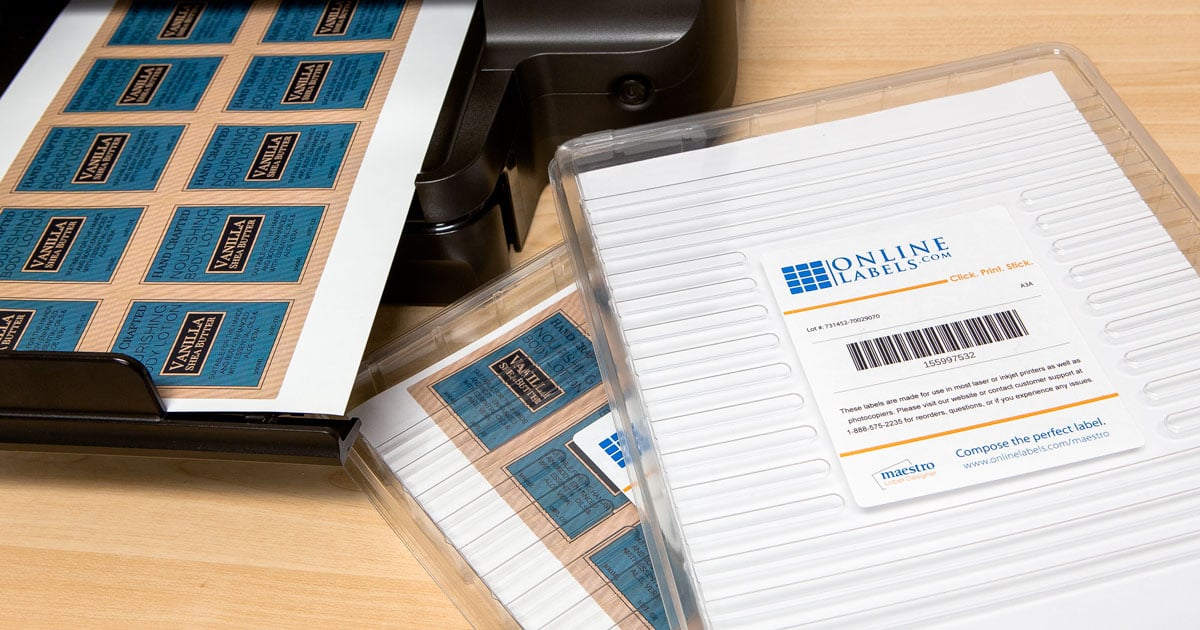
Label consistency starts before you even hit the printer – storing your labels properly can help keep them in prime condition. We recommend leaving your labels in their original packaging until you're ready to use them. Our rigid clamshells, durable envelopes, or cellophane wraps are designed to protect their integrity.
You should also avoid:
- Sunlight or heavy exposure to artificial light. These factors can result in discoloration or fading. If that can't be avoided, placing a solid cover over your labels can help prevent damage.
- Heat or fluctuating temperatures. Certain labels are fitted with our all-temperature adhesive making them more durable. For our standard materials, though, high temperatures can alter the effectiveness of the adhesive.
- Moisture. Long-term exposure to damp conditions can damage your label materials. Even waterproof labels should be kept dry before printing and application.
These tips apply to printed labels, too! If you're printing your labels all at once and applying them in batches later, you may run into many of the same issues. Printer ink can lose its vibrancy after sitting in the sun, for example. So be sure to keep your labels in proper storage conditions with consistent and vibrant labels.
Set Up Your Printer
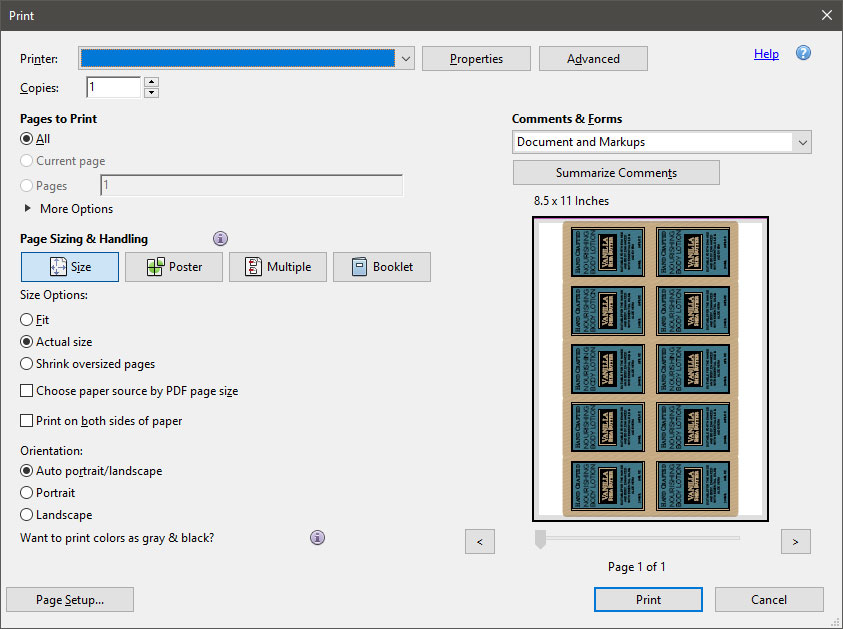
To help eliminate any changes as a result of your printer, run through the following checklist before you begin printing each set.
- Check your toner/ink levels. Ensure they start full or relatively high. If they run low during printing, you may notice some discoloration or lack of print coverage.
- Change the material setting (if necessary). Often times, you can get ideal results without having to change any settings. However, there are times when a special material setting may need to be selected. View our material setting recommendations.
- Deselect "Fit To Page" or "Auto Rotate and Center." You want your labels to print at 100% size and with the correct margins for proper alignment.
- Clean your feed path and rollers. Dust can affect how the labels are fed into the printer. Dirty paths can cause paper jams or leave roller marks down your label sheets.
Once you've verified the printer settings are correct, conduct a test print on blank paper. This will allow you to check alignment, ink levels, colors, and more.
Run Quality Checks
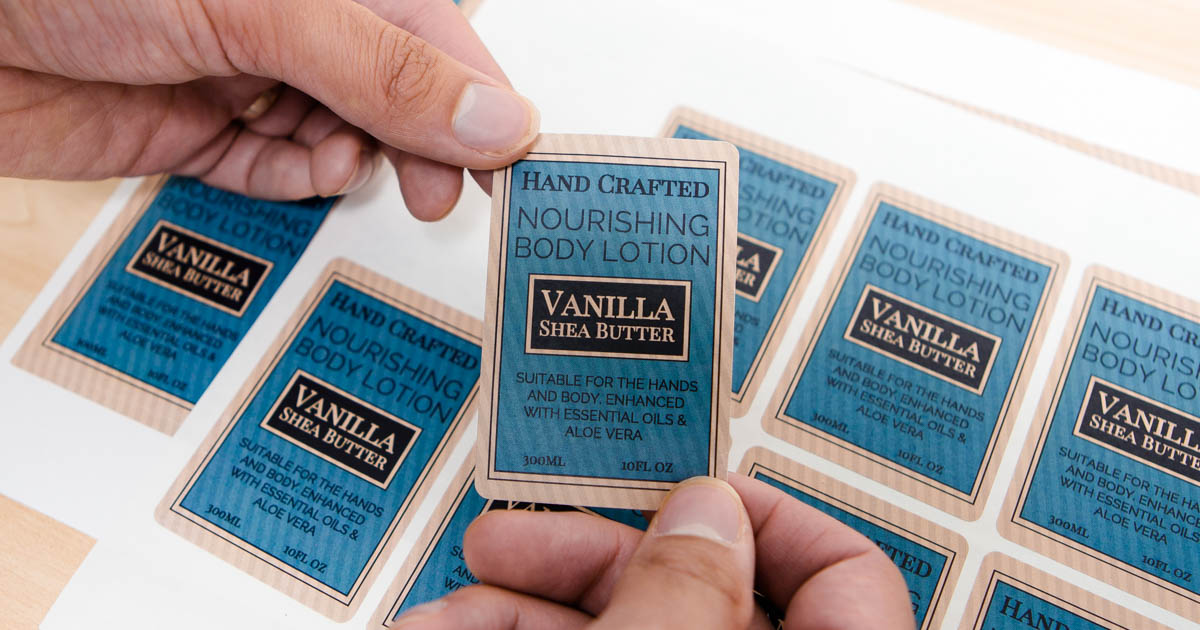
Whether you're printing all at once or splitting the job into batches, you may want to pull random labels off your printer tray for a quick analysis. In the professional printing world, this is called a press check. Issues can creep up and get progressively worse throughout the print job. Conducting checks to catch them early on could save you a lot of time and money.
Be on the lookout for:
- Shifts in the alignment of your design. As the label sheets get pulled from the paper tray into the printer, they may shift. This can result in prints that are slightly tilted or off.
- Streaking ink or toner. As you drain your ink or toner cartridge, your design may end up with streaks or inkless spots. You may also notice a gradual fade in the color across multiple sheets.
Clean Up
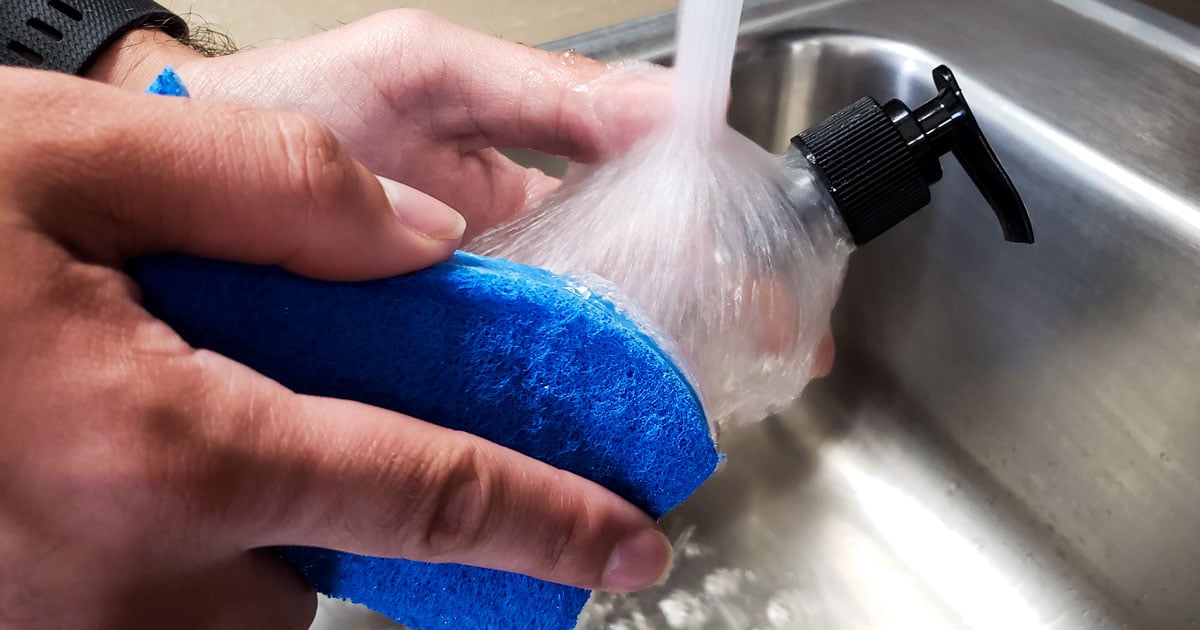
Wash your hands before you begin applying your labels. Your natural oils can degrade or interfere with the adhesive backing, affecting your long-term success. The labels will also bond best to a clean surface. The intended destination should be free from grease, dust, or moisture. Rubbing alcohol, all-purpose cleaning solution, or general soap and water will help maximize your adhesion.
Before moving onto the actual application of your labels, make certain that your hands and surface are completely dry. Residual water or cleaning solution can also jeopardize the stickiness of the labels.
Apply Your Labels
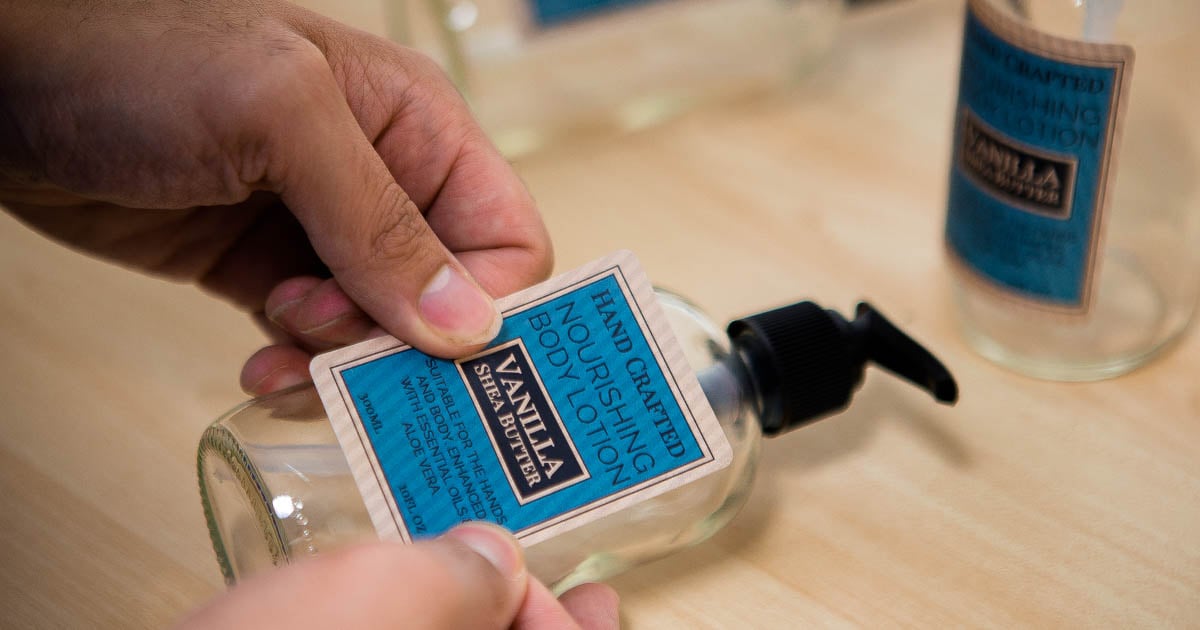
For the best finished product, follow these application tips. They'll help you avoid peeling, crooked, or bubbling labels and more.
- Pull the label away from the protective backing. Doing it this way (as opposed to pulling the backing from the label) helps eliminate any curling or bending while separating the sheets.
- Start application from the center. Once you have the middle down, apply pressure evenly through both sides. This is especially important for some round or cylindrical containers as it will help release tension and create a stronger hold. It will also help prevent bubbles and wrinkles.
- Smooth it out. Start smoothing the label from the center and work your way out. Small air pockets or wrinkles may fix themselves by the time you get to the perimeter.
- Keep an example of a perfect application. Having a finished product to reference is important. Without it, you may vary the starting point of application, direction, etc.
Replicate The Conditions
When it comes to labeling another batch of your products, it's important to consider how you did things the first time around. The temperature of your destination surface can play a big difference, for example. If you apply labels to a room temperature jar in batch one, but a cold jar in batch two, you may experience different results.
Enjoy the freedom that comes with printing your own labels and best of luck using these tips to keep your finished products consistent. You can see how other customers' products turned out in our Customer Ideas Gallery.