The Best Way To Pull Inventory and Package for Shipping
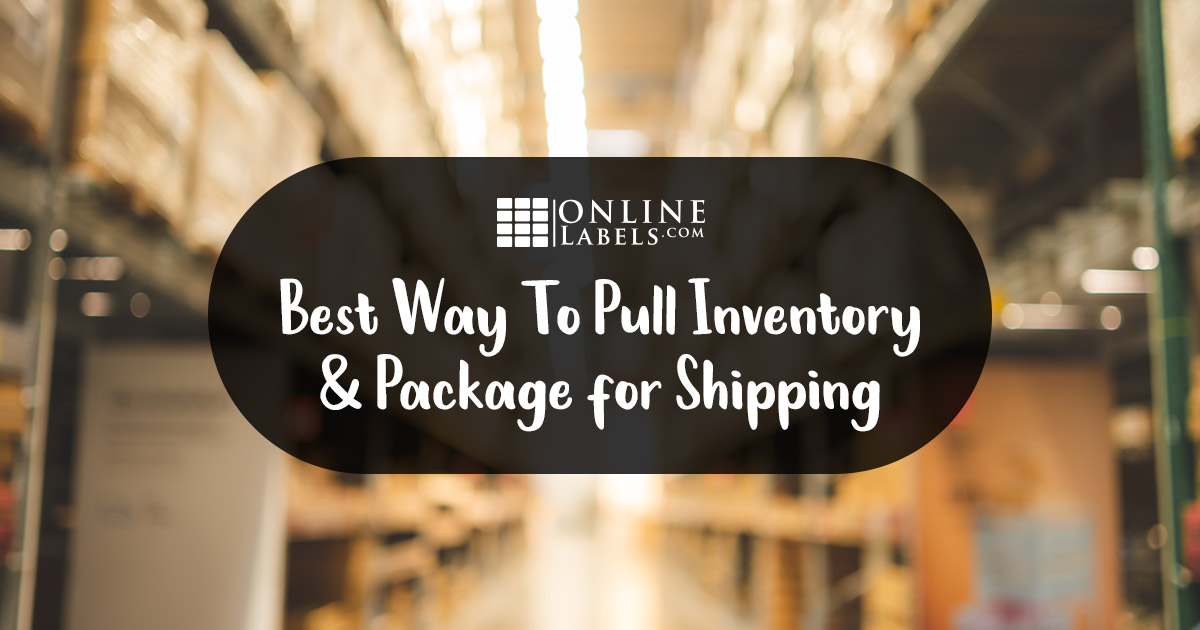
A growing business means a growing inventory. And with a growing inventory, it’s vital for your business to have a formal pick and pack system in place.
It may seem unnecessary to have a whole pick and pack procedure laid out — after all, you just pick the items your customer ordered from storage and pack them up to ship, right? That’s right, but with more structure and inventory labels, no matter the size of your business, you can avoid running out of items and help your business to run a lot more efficiently.
In this article, we’ll give you some basics for getting started with inventory management and tips on how to do it successfully.
Stay Organized
Keep your storage area neat and tidy, and have a designated bin or section of a shelf for each product. Bins and shelves should be clearly labeled, so when you look at a pick list, you’ll know exactly where to find each product. Keep it simple — labeling your inventory alphanumerically is an easy yet efficient way to stay organized. Give each section a letter, and each product within that section a number. For example, A1, A2, B9, etc. Have a lot of inventory? Consider keeping track of it with consecutive number labels.
It’s a good idea to store products that are sold together or variants of the same product near each other.
Invest in a Point of Sale (POS) Software
POS inventory systems are software tools used by retailers to process customer sales and track stock levels. They’re capable of counting inventory, tracking sales, providing basic reports, and more. Investing in one of these helpful softwares will really make a difference in creating a streamlined back-end procedure. There are so many to choose from, with each one having different features, and some even being free (with upgrades), so do some research and pick the one that makes the most sense for your business.
Note: Even though a POS software will keep track of your stock levels, it’s best practice to still do manual counts every now and then, to update numbers that may be off. Mix-ups happen, and products get lost, so counting manually is the most accurate way to stay up-to-date.
Have a plan and stick to it
Once you have a plan in place that works for you, be consistent with it to stay organized. But don’t be afraid to make adjustments as your business grows. A common pick and pack workflow that we’ve seen small businesses use is:
Print a pick list
This can be printed directly from your POS software, and is meant as a guide for whoever will gather the products for a specific order. The pick list should include order number, customer name and address, and product details, including what was ordered, the quantity ordered, and where to find it. Try to have one picklist for each order, so you can fulfill orders one at a time.
Pick the products
To keep things organized, have one person picking products per order, whether that be you or a warehouse employee. This picker will go around the storage room or facility, pick list in hand, gathering all the products on the order to be packed. If you notice you’re running low on a product, make a note of it on the pick list. Once you’ve picked all of an item, put a checkmark next to it.
Verify the products
With a printed invoice for reference, the packer will then look at the items that were picked and verify that it matches the sales invoice. The best way to do this is to scan each product into your POS software. If your products aren’t barcoded, the packer can do this by comparing SKUs or item names to the sales invoice.
Once everything is verified, print a packing slip using your POS software. This document basically contains the same information as the pick list, except the item location since this will be packed in the box for the customer to see. Only include what the shipment actually contains. So if there are any missing items, reach out to your customer and let them know that the item will be in a separate shipment.
Pack the products
This part is straightforward — pack all the items into a box, insert the packing slip, seal the box, and print a shipping label! Don’t forget to add some fun branding elements like stickers, personalized notes, coupon cards, and more!
We hope this simple guide to picking and packing products was helpful for your small business. Need labels to stay organized? Shop our collection of the most popular inventory label sizes.